The Japanese concept of monozukuri is somewhat of a buzzword right now.
Literally, it means ‘the making of things’, or ‘production’ and it’s the word Japanese people use to talk about manufacturing.
However, it has come to encompass much more than these translations denote.

In a broader sense, it means the synthesis or know-how, spirit of practices, and technological prowess. It’s all about artisanship and carries influence and weight.
When referring to the ‘spirit of practices’, we’re talking about the Japanese attitude towards making things with pride, dedication, and skill.
Essentially – It’s pursuing perfection and innovation. For these reasons, lots of people believe that monozukuri principles are the reason behind Japan being a world leader in the manufacturing markets.
Table of Contents
More than just manufacturing
If monozukuri meant making things and nothing more, then it’s like describing Da Vinci’s Mona Lisa as a picture of a woman – when we all know that it’s much more than that.
Monozukuri is more like a philosophy, a spirit, or a mindset.
It’s seeking perfection and a strong work ethic. It’s also a concept that is ingrained in many aspects of Japanese society.
Monozukuri etymology
The word monozukuri itself is an amalgamation of mono meaning “the thing” and zukuri “the production process.”
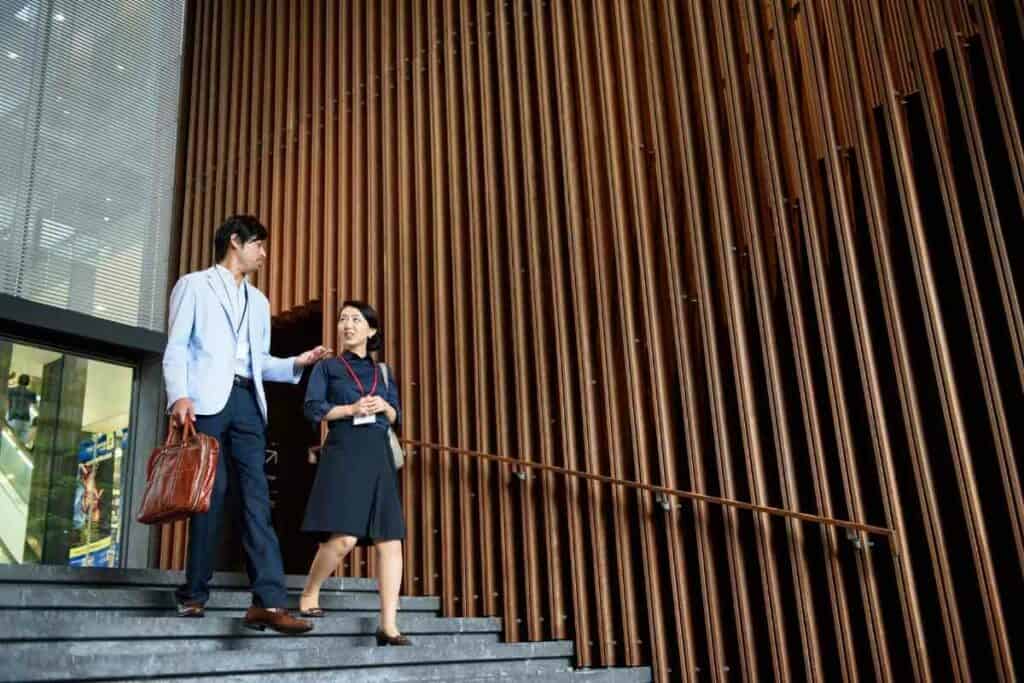
The word is pretty old and it’s a true Japanese word rather than one that has been borrowed from the West or China.
Throughout history, the word was used to describe craftsmen or artisans who took pride in their products.
As time went on, it began to be used more and more to describe production on an industrial scale.
In Japan – Working in a factory was not desirable. In fact, it was considered “3K”. This is a Japanese term that is short for kitanai, kiken, kitsui (hence the 3k!).
It translates to ‘dirty, dangerous, difficult’ and is a term that is used to describe typical blue-collar work that is better paid due to having undesirable traits.
The west has also adopted a variant and called it 3D.
Because of this implication that industrial production was dirty, dangerous, and difficult, the word monozukuri started being used to improve how the work was seen.
The car company Suzuki started using it to describe production in the 1970s, for example.
The word was boosted again in the late 1990s when the government promoted the image of factory work with a law called Promotion of Monozukuri: Basic Technology Promotion.
This law added significant value to modern manufacturing in terms of valuing artisans and craftsmen.
Examples of Monozukuri – Japanese Living National Treasures
If I asked you to name some famous writers, painters, or musicians, I bet you could name a fair few.
However, could you name a top weaver or carpenter? Probably not.
However, in Japan (alongside other artists, of course), there is a place for Living National Treasures aka Ningen Kokuho in crafts like dollmaking, sword making, pottery, textiles, woodwork, and such.
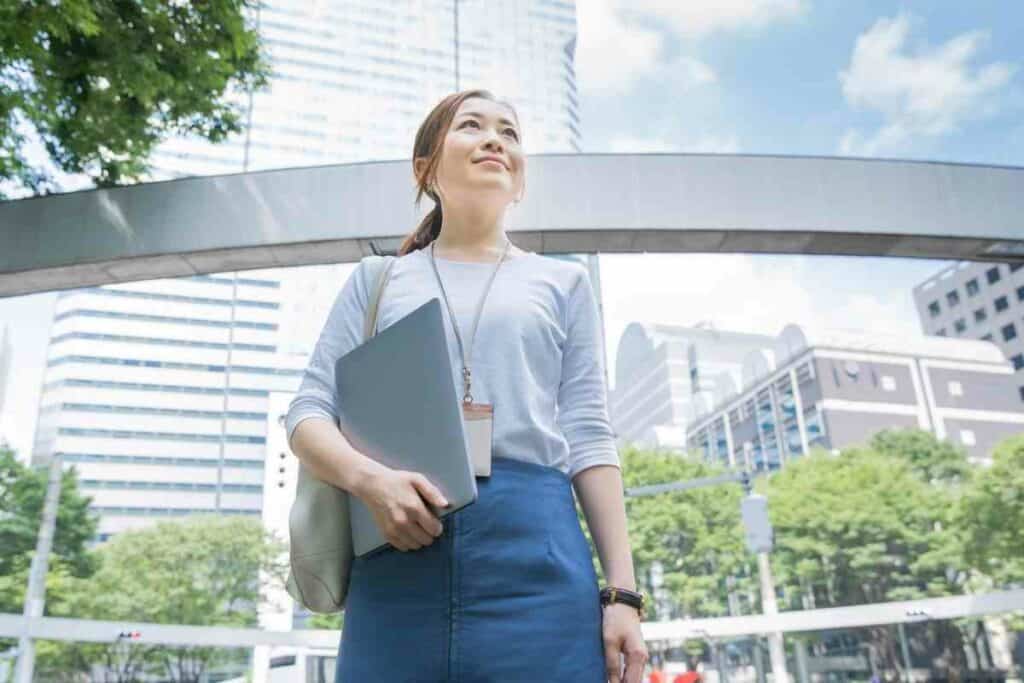
These artisans are respected in a similar way as traditional artists.
That’s not to say that these are household names, they’re not. They do, however, get respect and recognition for the skills they have.
Monozukuri, therefore, can be seen in this regard. It values the artisan and their artisanship.
Value for work
Japanese people also express the value of work in how they greet one another.
When you’re finished up for the day and are leaving the office, factory, or workplace, you’ll often hear gokurosama.
This means ‘thank you for your effort’ in the literal sense but it recognizes how demanding and hard the work is physically, even if you only work in an office.
This shows how much work is seen as a physical thing in Japanese society.
The principles of Monozukuri in the workplace
It’s not just about respect and admiration for work done, monozukuri is actually formed of principles that create the end result.
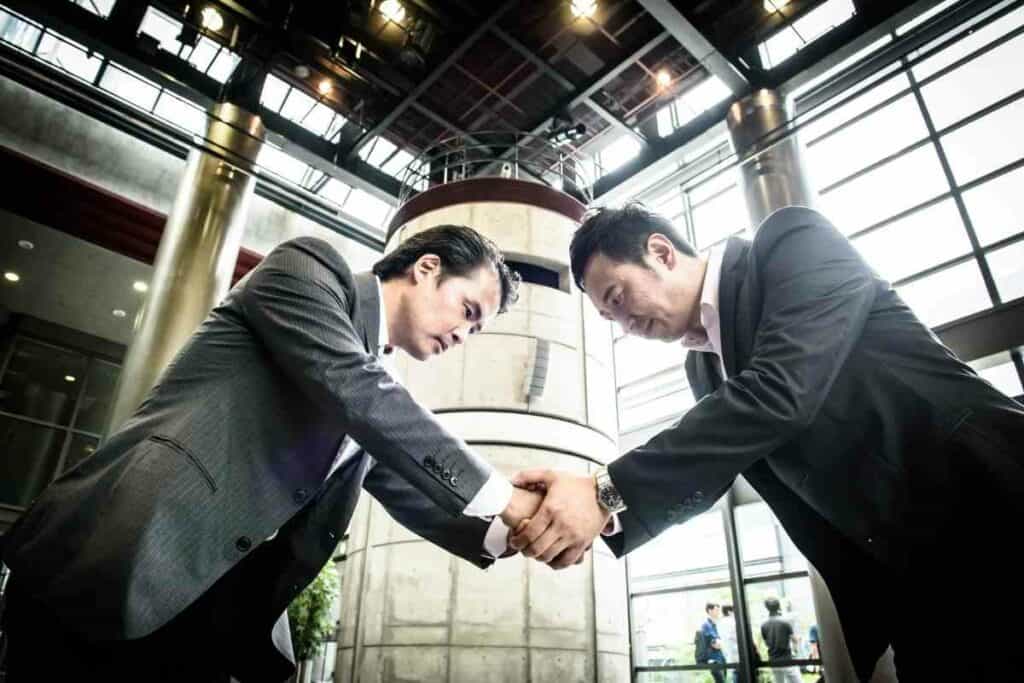
Essentially, monozukuri look to create a shift in how different structures within a workplace slot together.
There is somewhat of a dilution of the natural separation between different teams.
As a Result – All workers view themselves as a small cog in a big machine; they’re a common team and all tasks are as fundamental to the global aim as others.
There is room for interpretation in the monozukuri way of doing things.
There are no strict guidelines that organizations use when they choose to adopt the methodology and mentality.
There are, however, fundamental principles.
To start with, there is a constant striving to improve work processes. The end goal is to create the highest quality product with the best efficiency.
Solving problems, the monozukuri way
When problems arise, however, there are certain processes, allowing for a learning curve towards improvements.
Troubleshooting is not just the responsibility of the management or one person, but the whole team.
All team members will know the process and need to involve themselves in working out the cause of any problems.
They then work to eliminate them and work to find an improved system. This strive for improvement doesn’t stop; there’s no if it ain’t broke don’t fix it mentality here.
The idea is that there will always be something better that we can do.
Competitors
This constant striving for improvement also encompasses looking at competitors and learning from them.
Understanding how competitors work means places of work can optimize their procedures to become more efficient and produce better products.
Adaptations to the monozukuri way of doing things
As we’ve expressed, there is no rigidity in the way monozukuri happens in the workplace.
This means its basic principles have been taken on in various guises around the world.
One popular adaptation is Monozukuri Genba. This is an adaptation of the methodology for those working in tropical environments.
Monozukuri Genba uses Latino passion to achieve work discipline.
This is a system with levels to seek maximum efficiency and works for people living in tropical climes.
The levels of Monozukuri Genba
This adaptation has four levels, which all seek to achieve objectives of their own.
Each level needs to be applied correctly before an organization can move up to the next level for the most powerful results.
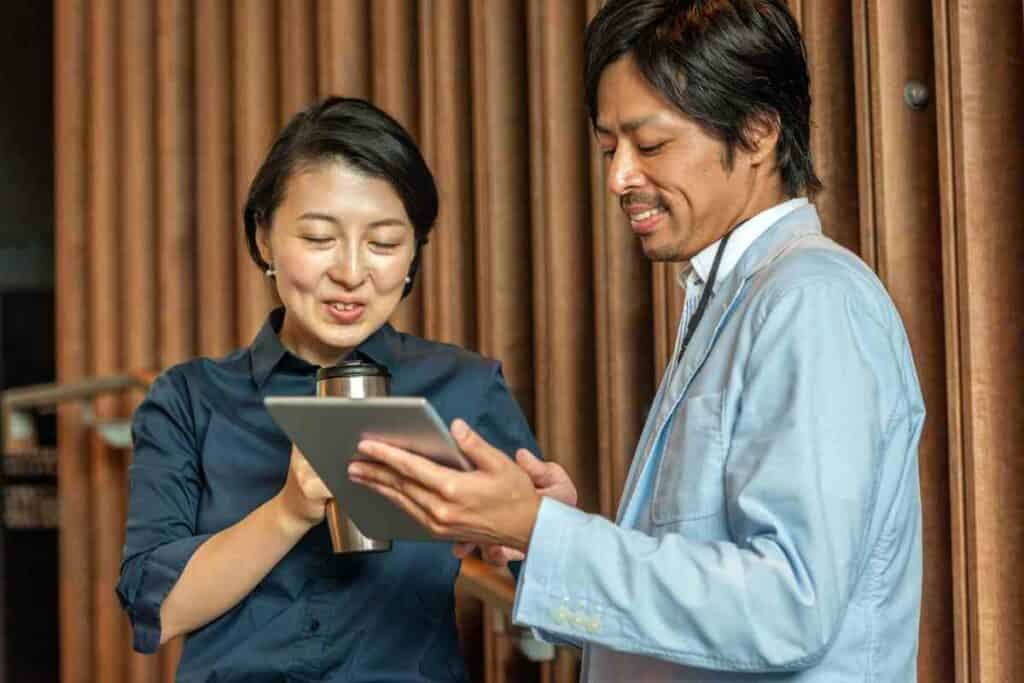
Let’s take a look at the levels of Monozukuri Genba.
Standardization
The first level of Monozukuri Genba is standardization.
At this level, workplaces seek to standardize all positions in the company.
They look for the maximum discipline and skill of all workers. It lays down the foundations for the next steps.
Methodology
When the second level is undertaken, employees are given some methodologies to help them learn how to analyze work processes.
They learn to detect and solve problems optimally. The methods used will depend on the industry types and the workers too.
The most popular of methodologies is QRQC, which is an English acronym meaning Quick Response Quality Control.
This method looks to optimize business response times in problem solving so when a problem is detected, there is a standardized procedure that workers follow to solve the issue quickly.
Improvement
At level three, the idea is to improve how the Monozukuri Genba principles are used.
At this stage, another methodology is used. This is called Kaizen, which is Japanese for “improvement”.

The company’s unique situation will apply kaizen the concept in different ways.
Kaizen applies to all workers from those on the assembly line, right to the CEO.
It also applies to all processes, including things like logistics, and purchasing, etc.
Kaizen Works Everywhere – From government, banking, psychotherapy, and healthcare. There are no industries where this concept can’t be applied.
Capitalization
This is the fourth and final level of the Monozukuri Genba methodology.
This is achieved when all of the improvements made during the Monozukuri Genba process are effective.
At this point, the company or organization is ready to compete at a high level in its industry.
Final thoughts on Monozukuri art principles explained
As we’ve seen in this article, Monozukuri art principles apply to lots of areas of society and lots of different sectors.
What was once a term used to describe the artisan or artisanship, has now spread globally as a methodology for many businesses and organizations to adopt – such is its success.
What we mustn’t forget, however, is that Monozukuri is truly Japanese in its essence.
Of course, other nations can adapt the principles to their own situations, and they can do so with great success.
Having said that, monozukuri just simply can’t be replicated elsewhere wholly. It really is something that you need to experience in the land of its origin to capture its true uniqueness.
Also Useful
- 12 Things Tourists Should NEVER Say in Japan
- Kissing Robot: Exploring the Popularity of the Chinese Kissing App
- Unlocking the Secret Dating Rituals Only Locals Know in Japan
- Samurai Armor: Ancient Protection for Japan’s Elite Warriors
- 10 Amazing Facts About Schools in Japan: Unique Traditions and Educational Practices
- Where can you see snow monkeys in Japan: Best locations and viewing tips